In the previous installment of this two-part series, we looked at common slab settlement danger zones, causes of sinking slabs, and the many risks of neglecting a known trip hazard. This time around we’ll review the two most common non-polyurethane repair options, and then explore the three most common types of polyurethane slab repairs.
Non-Polyurethane Repair Options
Aside from polyurethane repair, the property owner has two other options: replacing the slab or mudjacking it with cement grout. There are drawbacks for both.
Tear Out and Replace
Ripping out a slab and putting in a new one has three main disadvantages. Namely, the process is…
Environmentally unfriendly (landfill bound?).Messy (requiring heavy equipment and possibly damaging the surrounding area).Time consuming.
Mudjack with Cement Grout
📷Mudjacking may be less expensive than replacement, but the property owner is still facing a number of issues.
It’s still a messy process.Cement grout washes out.The grout is heavy and can sink over time.The grout can crack and shrink over time.Not an impermeable water tight solution.
Structural Polyurethane Repair
Polyurethane repair has distinct advantages over replacement and mudjacking.
Very clean installation process.Lighter than cement mudjacking grout and won’t sink over time.Will not shrink.Closed cell structure makes it water impermeable.Typically less expensive than replacement.Less time consuming to apply than a mudjacking or replacement solution, and ready for traffic 45 minutes after application.
Not to mention the strength of these polymers. For more on that subject, see our blog post Slab Jacking with Polyurethane Foam - How Strong is Strong Enough?
Trip hazard repair with polyurethane resin can require one or a combination of the following three approaches: lifting, soil stabilization and void fill. Let’s take a close look at all three…
Lifting
Sunken concrete slabs can be lifted back into place with a-two component structural polymer foam designed to work in wet or dry conditions. The expansion force of the foam coupled with the pressure of a PMC proportioner pump can generate enough controlled force to lift virtually any structure back into position within 1/10” of the intended level.
Soil Stabilization
Unstable, eroded, or loose soil below infrastructure can result in settlement, damage to the structure above, and of course – trip hazards. Voids can be filled, soil consolidated, and water migration halted by permeating the soil with one of our ultra low viscosity polymer resins. Once the bearing capacity of the soil has been increased with this process (soil has been stabilized), then the structure can be lifted with our slab lifting process.
Void Fill
Water erosion beneath slabs can cause voids to form that weaken the structural integrity and allow higher water pressure to develop. Filling these voids with rapidly expanding foam that is designed to react in the presence of water will return the integrity to the structure and prevent trip hazards. We have polyurethane resins designed specifically for this type of application.
Whether you’re a property owner looking for a professional to repair trip hazards on your property, or a contractor looking for material and/or technical assistance –Level Home Foundation Repair is at your service. Give us a call at 918-361-7787 to discuss your trip hazard concerns. S
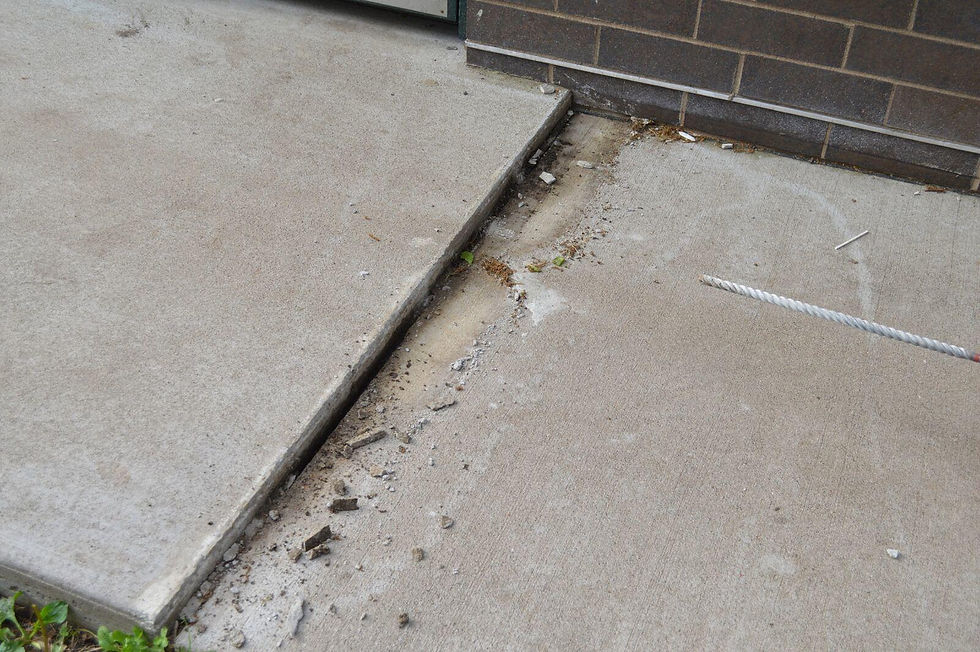
ee our official website visit: www.levelhomefoundationrepair.com
Comments